
Central Research & Development Center
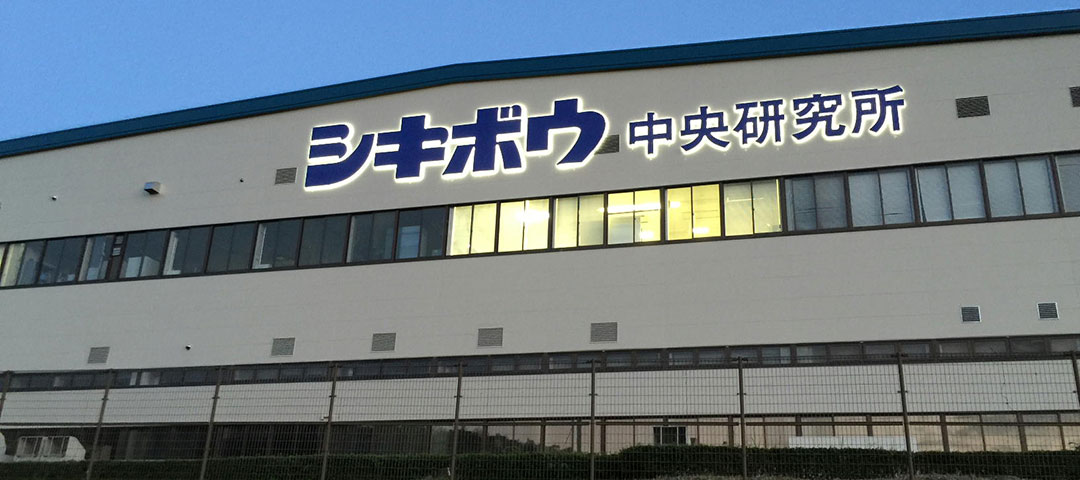
At our Central Research and Development Center, we have been developing fiber reinforced composite which has the properties at light and strong and their reinforcement (preform) which is based on textile technique and experience.
Recently, we have been developing new materials aimed at carbon neutrality.
Textiles
1.improvement for fiber shape and properties
We are carrying out for study the adding the fiber property of composites such as improvement of surface treatment at Carbon and Glass fibers, twisting yearn and mixed spinning.
2.Consideration for the environment
We are moving forward with research into natural textiles (cotton yarn, hemp, silk, cellulose nanofiber), textiles that consider the environment (for example, Offco Nano), and recycle textiles that are suitable for composite materials.
Resin
1.improvement for resin property
At Shikibo, we are developing the improvement of matrix resin.
In particular, we developed a nano-composite material that is combined micro-silica to resin for improvement the fracture toughness of matrix property.
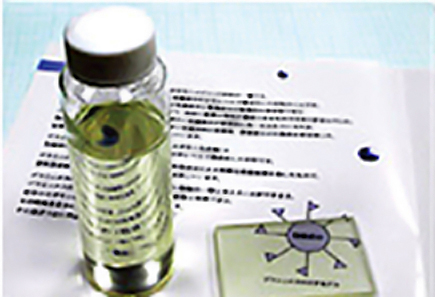
Improvement Matrix property
Plamix: Nano Composite
Improvement resin which is combined silica fine powder into epoxy resin.
2.Blends
We are developing the original blend resin to improve resin property for viscosity, glass transition points, toughness, and more.
3.Development of ecological materials
We are developing the new resin that is combined natural ingredients.
Substrates
1.Development of fiber arrangement for reinforcements of composite.
We can be arranged the fiber to various shape to selected fiber direction, length, ply thickness and others in freely.
Since the fiber can be arranged freely, the fiber can be possible to align around the curved shape.
"The fiber can be arranged around the hole for reinforcement the hole strength.
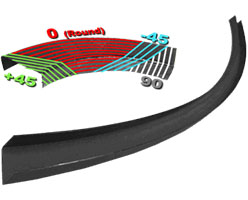
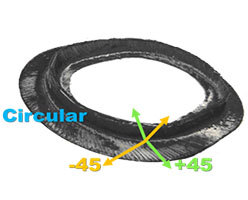
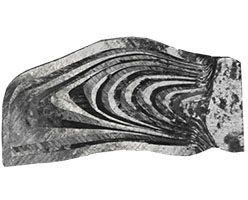

2.Development of textile preform
We can provide various types preform, from thin to thick one.
We can provide 2.5D textile preform that is arranged the fiber in three dimensional architectures.
"We can 3D textile preform that fiber can be arranged through the thickness direction.It can be also provided complex shape preform."
It can be also provided preform by using very brittle fiber such as ceramics.
2D Complex Shaped Preform
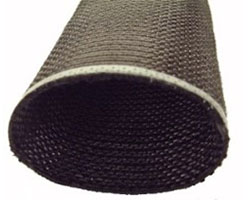
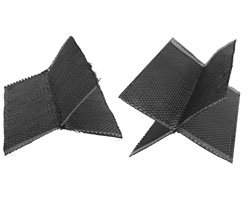
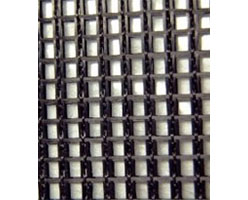
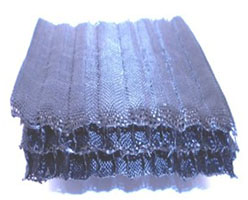
3D ( Three dimensional ) Preform
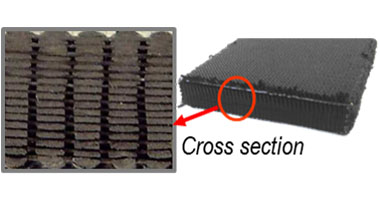
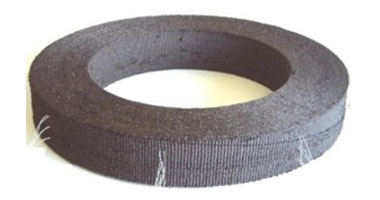
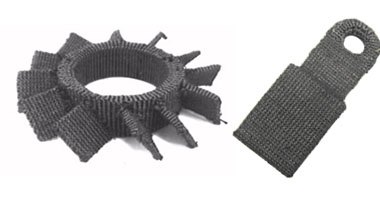
Research and development for CMC materials for 1400℃ Class.
We Shikibo is developing the turbine parts by using Ceramic-Matrix Composites (CMC) for next generation aircraft engine parts, with IHI and UBE as joint research.
Shikibo is developing the reinforcement of CMC at 3D preform by using SiC fiber.
3.Development of through the thickness reinforcement for composite.
We are developing not only 3D preform but also other reinforcement method for through the thickness direction (Z direction).
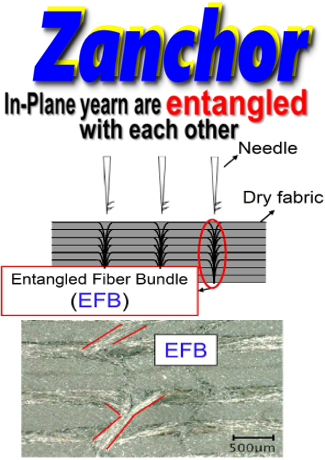
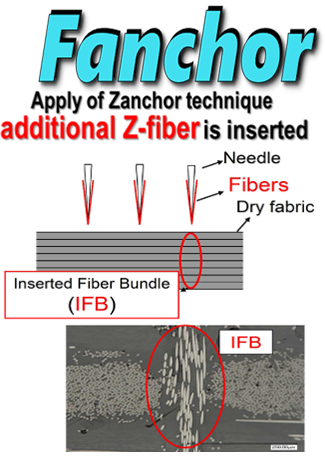
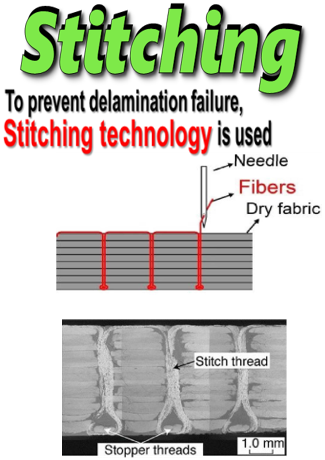
-
Limit impact delamination propagations
-
By using the Zanchor process the composite part showed higher G1c value which demonstrate higher delamination resistance.
The fiber bridging occurred after the DCB test in Zanchor composite.
This fiber bridging causes higher fracture toughness.
-
Improve compression-after-impact(CAI)strength
-
< Higher impact damage resistance >
Result for Impact damage test "Zanchor" composite showed higher CAI value which is an important property for composite aircraft structures.
-
Dramatically increase the permeability of the entangled fiber structure
-
Zanchor preforms exhibit higher resin flow speed at Z direction.
Because Zanchor has through the thickness fiber, so the resin is flowed through the z direction fiber.
Composite Materials
1.Thermosetting composite materials
We are developing various types process method for composite materials.
2.Thermoplastic composite materials
We are also developing the composite materials for recyclable and environmentally conscious.
3.Ceramic materials
We are also developing new processing methods for advanced composite materials such as CMC and C/C.